Lifecycle Services
We use our experience as a leading process systems provider to boost the value of operations, maximize uptime, and improve performance in operations around the globe. Our lifecycle services team are your partner for the full lifetime of your processing equipment and field.
The assurance in performance
The lifecycle services offerings are based on our extensive processing technology expertise within the areas of oil, gas, water, and sand treatment including specialized technologies such as MEG reclamation and seawater membrane filtration.
Lifecycle Services
We serve customers post-delivery of processing equipment and systems, including:
- Installation, commissioning, and start-up support
- Preventative maintenance and inspection
- Operational support
- Healthcare agreements
- Remote support and digital monitoring
- Operator and process training
- Spare parts management and supply
Our Experts
We service all processing equipment including those supplied by others. Our engineers are located globally and our involvement on site ranges from providing site personnel for specific activities such as membrane, internals, bushing, or liner installation to full site installation, commissioning, and operational teams.
Our aim is to ensure the equipment we deliver is preserved, commissioned, and started properly. Our lifecycle services teams engage early in the project phase to define the most efficient commissioning and start-up procedure. Acknowledging that every oil and gas field is different, commissioning and start-up is not to be considered a commoditized process. Our teams can address any challenge arising and to fine tune the operational parameters of process equipment to the requirements of each field.
Healthcare Agreements
As operational conditions change over time, recurring process and site support is necessary to maintain optimal production and reduce risk. We offer these services on call or most efficiently through a healthcare agreement. This allows us to optimize performance, share knowledge, and maintain reliability of the systems. The agreement typically includes operational support, performance review, extended process warranty, training, spare parts management, and regular scheduled follow-up activities at site. This allows for seamless solutions to be provided for process optimization and revamps and extended guarantees of the units if required. Through regular service and maintenance, we can detect weaknesses or operational changes early to avoid escalation.
Process Intelligence Manager
We have a long history of providing digital and process technology solutions to the oil and gas industry. Through a combination of these track records, we have created our Process Intelligence Manager offerings to enhance the visibility of current and historical performance – and to enable the deployment of data science to generate new Process Intelligence Insights into system performance and health status. These include early detection and differentiation between various production issues, which together with recommendations for mitigation ensures that issues can be addressed prior to becoming severe.
Training
We have established technical and operational training programs to ensure operations meet the highest performance and safety standards. The programs can be provided in a classroom or remote environment by our expert trainers to enable direct exchange of know-how and field experience to engineers, operators, and maintenance personnel. A comprehensive library of standard, approved training programs has been developed over many years encompassing lessons learned and operational experience. Specialized training programs can also be designed for customers based on their specific needs and knowledge levels.
By carrying out regular operator training we aim for a continuous and high level of safety and competence for people, while in addition transferring best practice knowledge on our areas of expertise.
Spare Parts
We understand the importance of spare parts to the smooth operation of units. Our service is built on a foundation of superior planning, top quality standards, cost-effectiveness, quick reactivity, and thorough support. We work with our customers from early stages to plan the best but lowest range of stock to hold to minimize any shut-down or failure risk.
Parts quality plays a big role in process guarantees, and we can offer extended guarantees by coupling parts management to a healthcare agreement.
Legacy brands and companies we support
With the wealth of brands and products acquired over the years, our lifecycle services team are primed to support these products and systems that were delivered. Continuity of your operations is guaranteed with our obsolescence management of our product portfolio including stock management, maintenance of archives and retention of developer level know-how in our teams.
Legacy brands and companies:
- Paladon Systems
- Opus
- Merpro
- APS or Aker Process Systems
- AKPS or Aker Kværner Process Systems
- SSI (Separation Specialists)
CO2 Removal Unit Training FlyerTraining in CO2 removal with hollow fiber membranes
Electrostatic Coalescer and Desalter Training FlyerTraining in Electrostatic Coalescer and Desalter technology and process
ePack Technology Training FlyerTraining in ePack technology, efficient operation, and maintenance
Gas Dehydration Unit Training FlyerTraining in Gas Dehydration Unit process, operation, and maintenance
MEG Loop Chemistry Training FlyerTraining in MEG Loop Chemistry principles and operational procedures for a slip stream system
MEG Recovery Unit Training FlyerTraining in operation and maintenance principles of MEG Recovery Units
Offshore Produced Water Treatment System Training FlyerTraining in offshore Produced Water Treatment technologies, system operation, and maintenance
Seawater Treatment Unit Training FlyerTraining in Seawater Treatment Unit overview, operation, and maintenance
ToreScrub Sand Handling Unit Training FlyerTraining in ToreScrub Sand Handling Unit, operation, and maintenance
ToreTrap Desanding Hydrocyclone Training FlyerTraining in ToreTrap Desanding Hydrocyclone technology, operation, and maintenance
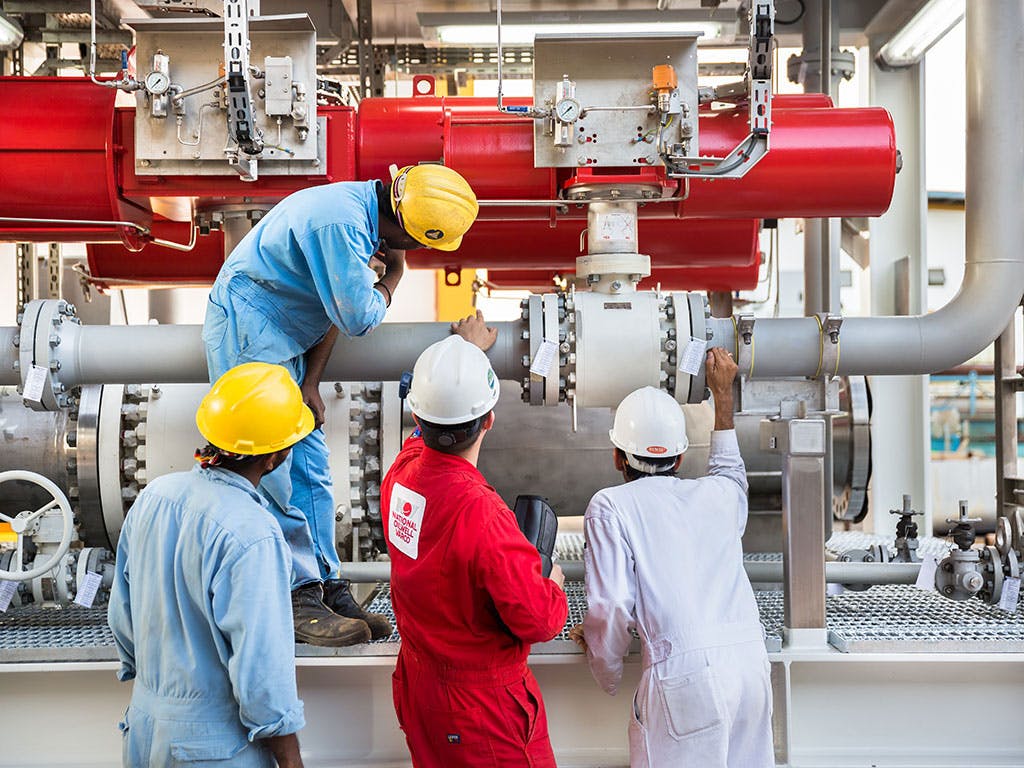
Commissioning
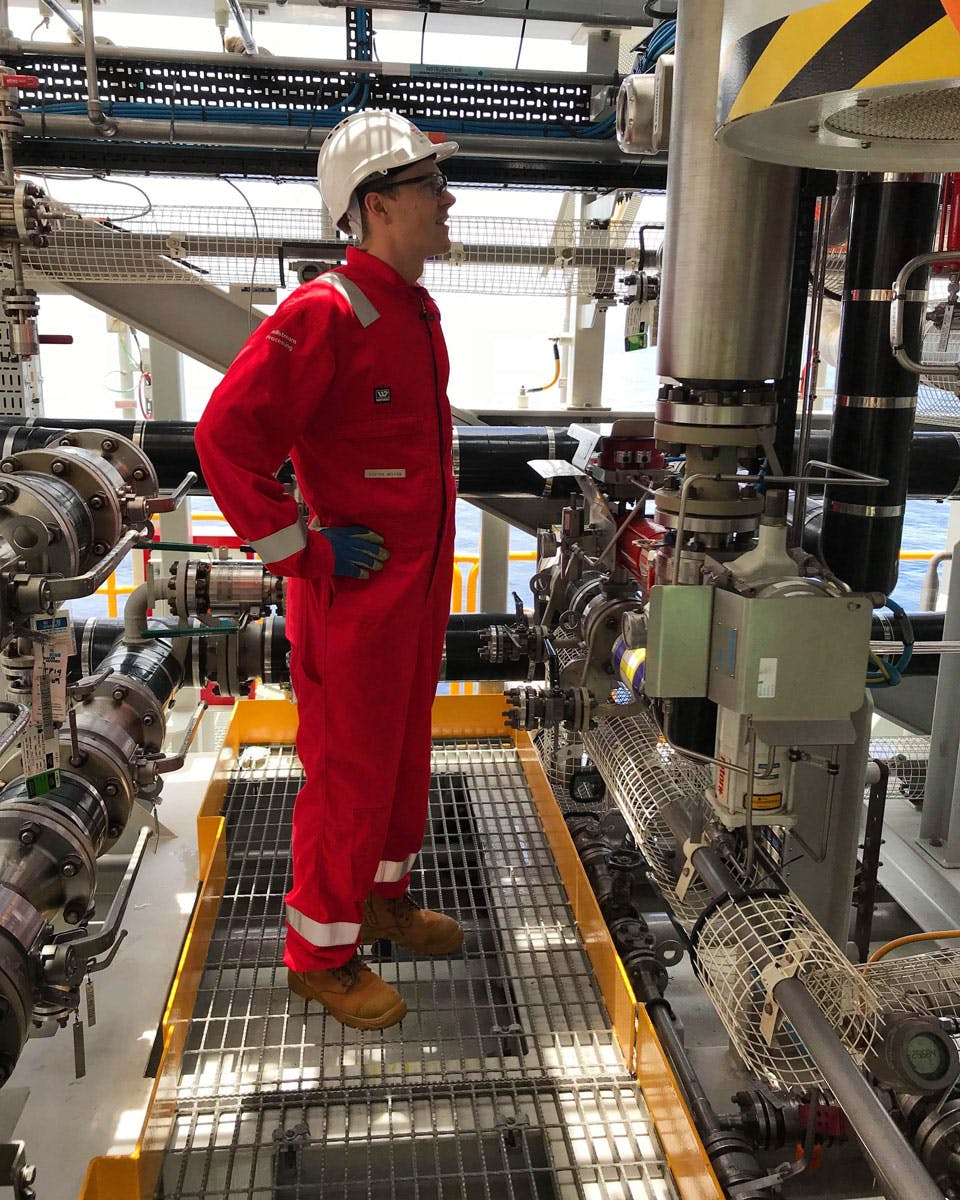
Healthcare
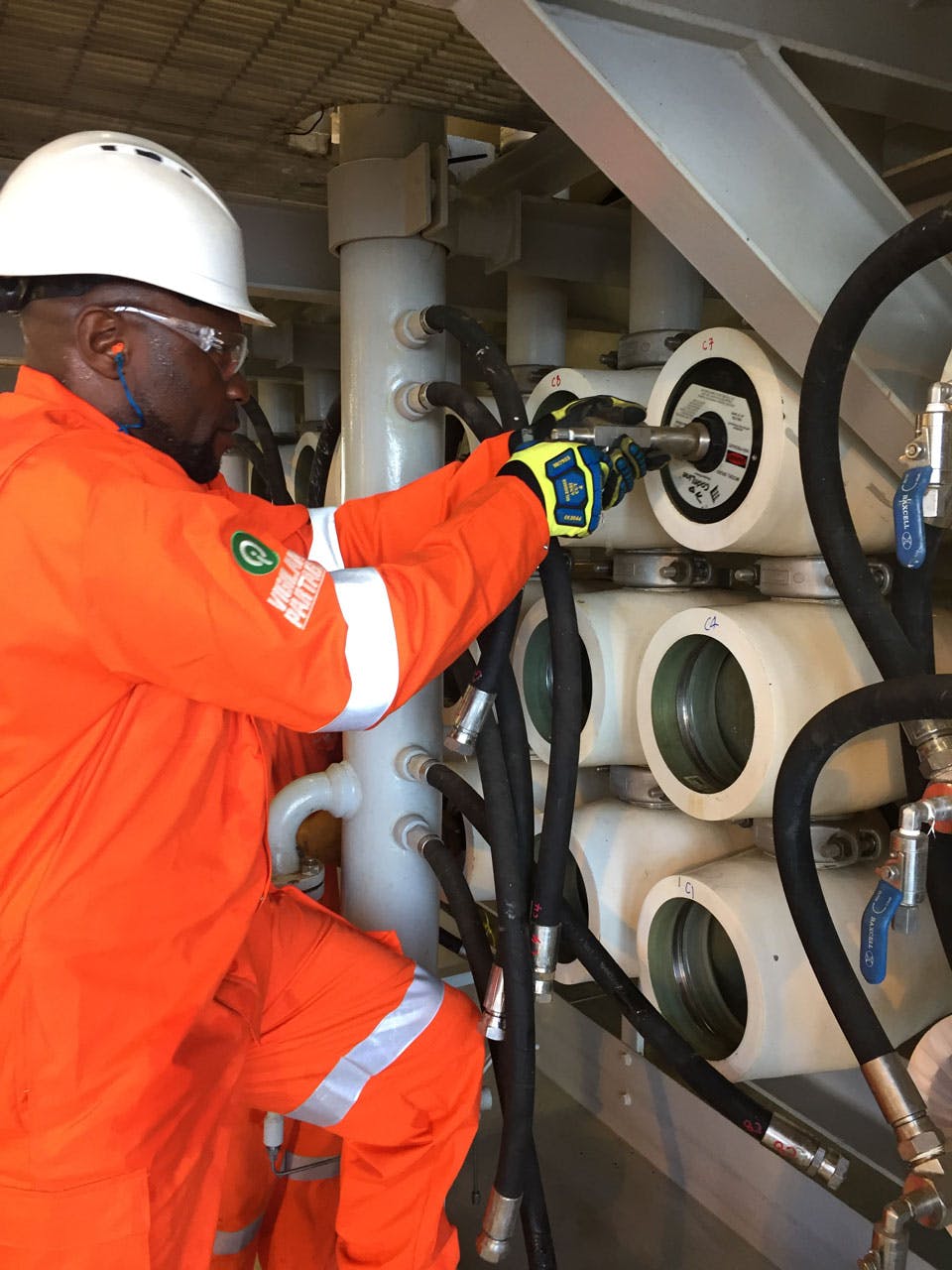
Spare parts
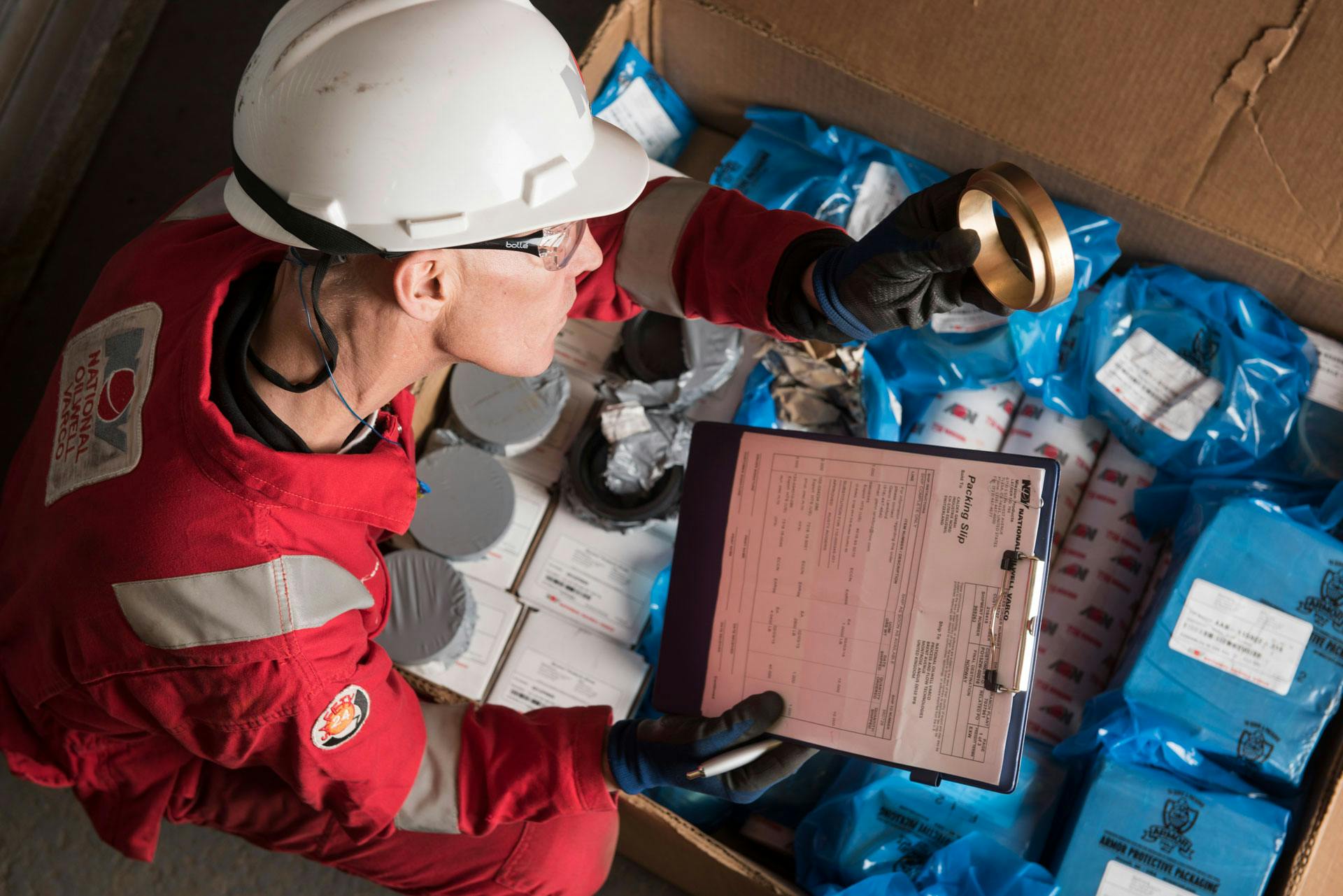
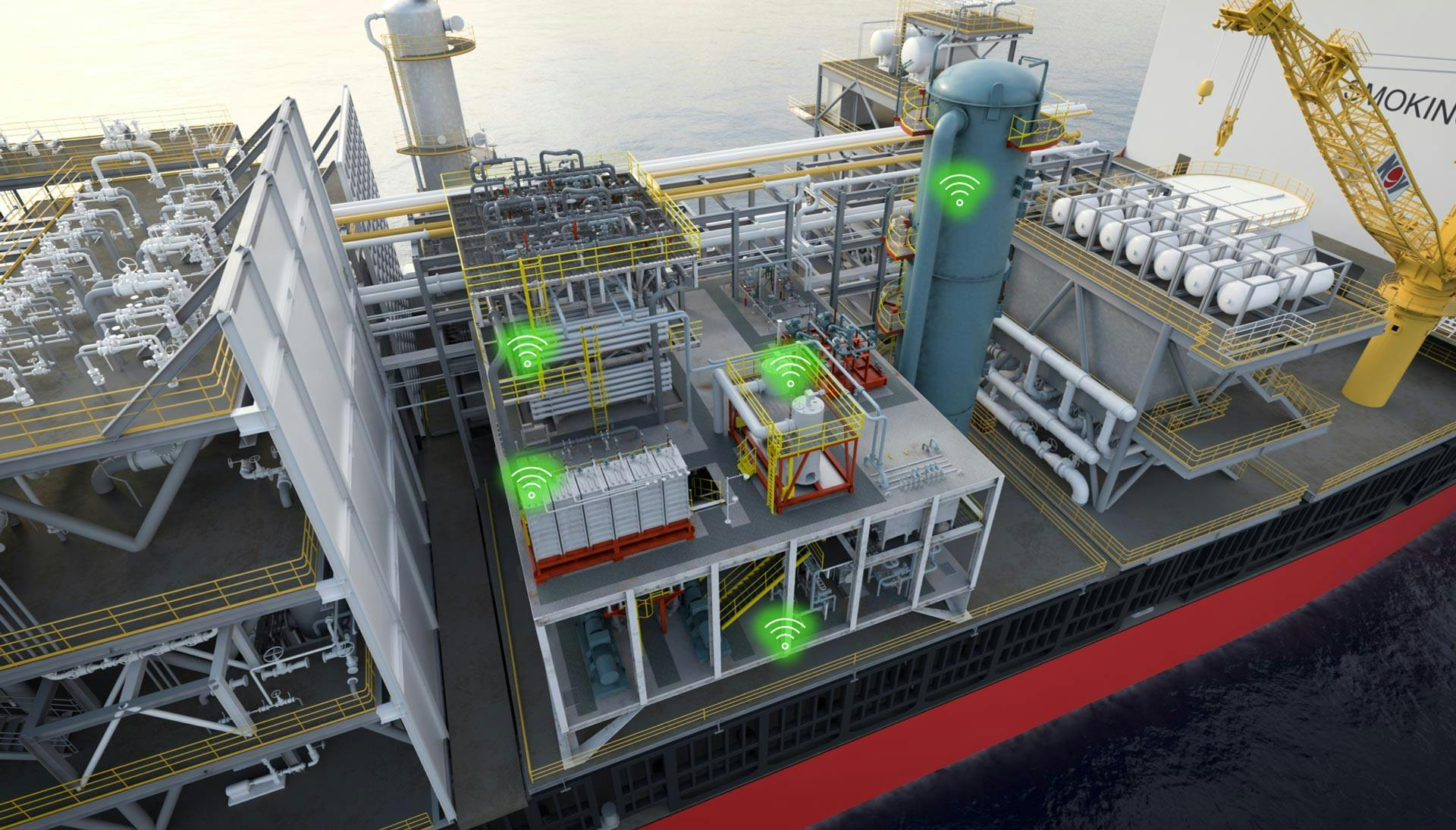
Process Intelligence Manager
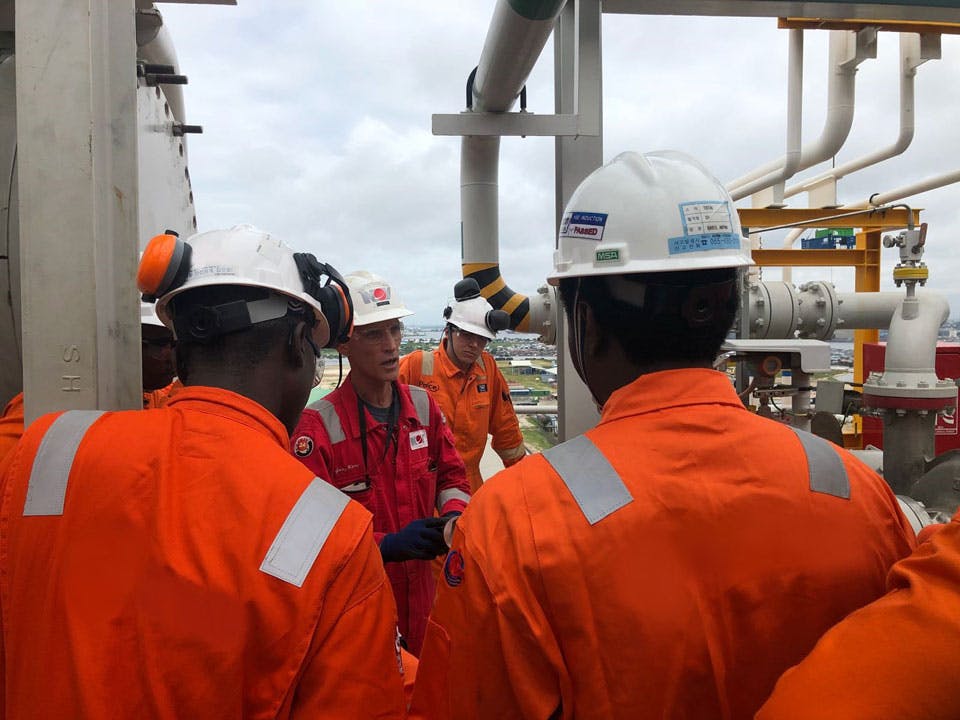
Training
Related Products
Process Systems
We deliver equipment and solutions to the upstream oil and gas industry for the separation and treatment of oil, gas, solids, seawater, and produced water.
Seawater Treatment
We have been the market leading supplier of seawater treatment technologies for over 30 years and can provide tailored solutions to suit any project.
MEG Recovery
We provide an extensive portfolio of MEG technologies developed on decades of field-based experience and extensive research by our team of subject matter experts.
Brownfield Solutions
We optimize process systems, remove production bottlenecks, improve environmental performance, and support operations through a global network of specialists and a commitment to service.
Process Intelligence Manager
Our Process Intelligence Manager for remote process optimization and condition monitoring enables our clients to reduce their operational expenses through extending lifetime of equipment, increasing system availability, and optimizing utilities consumption.