Intervention and Stimulation Aftermarket Solutions
Reduce total cost of ownership of your coiled tubing, stimulation, acidizing, wireline, sand handling, and cementing equipment with our aftermarket solutions.
We understand what it takes
At NOV, we know how critical it is for your equipment to operate at peak performance. To ensure reliability throughout your equipment’s life, we offer extensive product maintenance programs that are customized to your needs and updated as the industry evolves. Our processes are simple, transparent, and created with your success in mind.
To support thousands of pieces of equipment working around the world, we established an integrated network of strategically located facilities to provide technical support, field service, repair, spare parts, training, rentals, and field engineering. With a professional support team available 24/7, we’re always there when you need us — keeping your equipment running longer and your customers satisfied. Explore what we can do to protect your investments.
Aftermarket Solutions: Stimulation, Acidizing, Coiled Tubing Support, and Cementing Equipment Brochure
Aftermarket Solutions: Coiled Tubing, Nitrogen, and Snubbing Equipment Brochure
Global Coiled Tubing and Nitrogen Equipment Contact List
Pressure Pumping and Cementing 24-hour Support Contacts
Global Wireline and Flowline Contact List
North America Wireline Services and Aftermarket Brochure
Recommended WPCE Service and Certification Schedule Reference Guide
Elmar Service and Recertification Reference Guide
Elmar Pressure Testing Standards Reference Guide
Rolligon Aftermarket Service Packages Flyer
Rolligon Training Classes Flyer
Texas Oil Tools Global Service Center Contact List
Texas Oil Tools WCE Inspection and Recertification Flyer
Wireline & Flowline Training Services Brochure
Aftermarket Solutions

Coiled Tubing, Nitrogen, and Snubbing
Learn more

Digital Completion Solutions
Learn more

Wireline and Flowline
Learn more
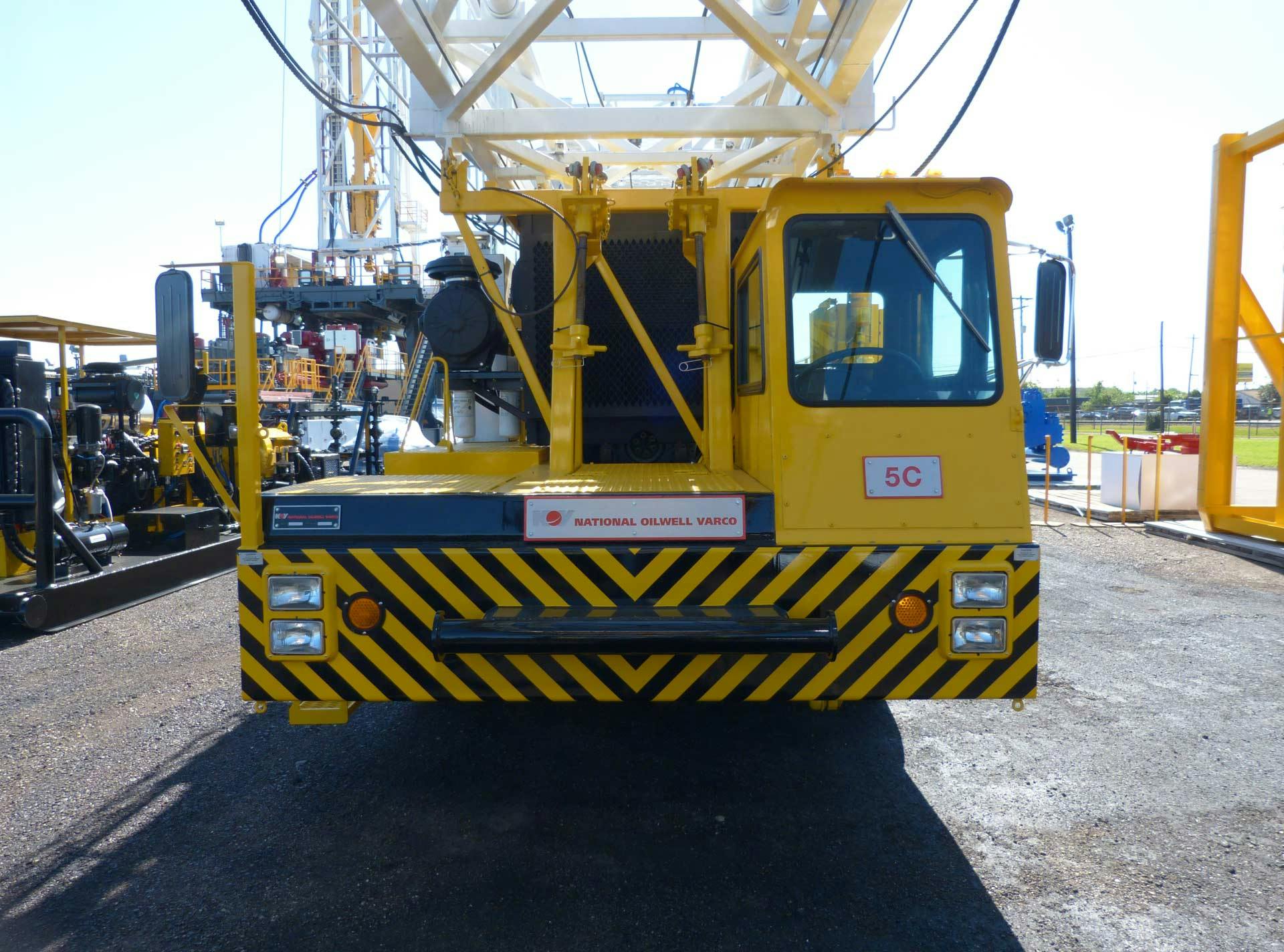
Mobile Rig
Learn more

Pressure Pumping
Learn more

Cementing
Learn more
Our Offerings
Select an offering to learn more
Need Aftermarket Support?
We provide world-class 24/7 support to our customers.
Please contact us at the below emails:
[email protected][email protected]
[email protected]
[email protected]
[email protected]
[email protected]
Related Tools
