BW Offshore, a leading global provider of floating production services to the oil and gas industry, had commissioned construction of various components of the Catcher Development floating production, storage, and offloading (FPSO) vessel for deployment in the North Sea. The Catcher Development FPSO, which has a processing capacity of 60,000 bopd and a storage capacity of 650,000 bbl, is set to deliver first oil for operator Premier Oil UK in 2017. The specific design of the FPSO called for increased resistance to the North Sea’s harsh environment, industry-leading safety standards, and an innovative approach to produced water treatment, seawater treatment, and water injection for improved oil recovery.
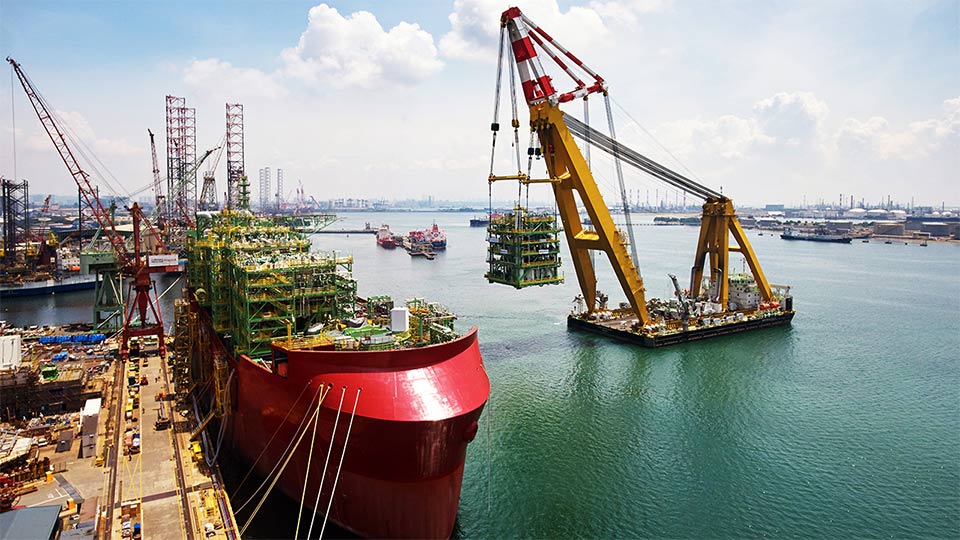
The Catcher Development FPSO was designed with resistance to harsh environments and to the highest safety standards to ensure longevity in the North Sea.
NOV was approached by BW Offshore to build a seawater and produced water treatment module to meet the water-injection requirements of the FPSO over the life of the Catcher Field. The module utilizes nanofiltration membranes for seawater treatment and a proprietary produced-water technology, which consists of deoiling hydrocyclone liners, degassing vessel internals, and a compact flotation unit. The system can inject produced water, seawater, or a combination of both to enable waterflooding, enhancing recovery and maintaining optimal performance. By removing hydrocarbons from produced water and solids and sulfates from seawater, the injection water is treated to good composition, ensuring well injectivity to maintain pressure during the lifespan of the reservoir.
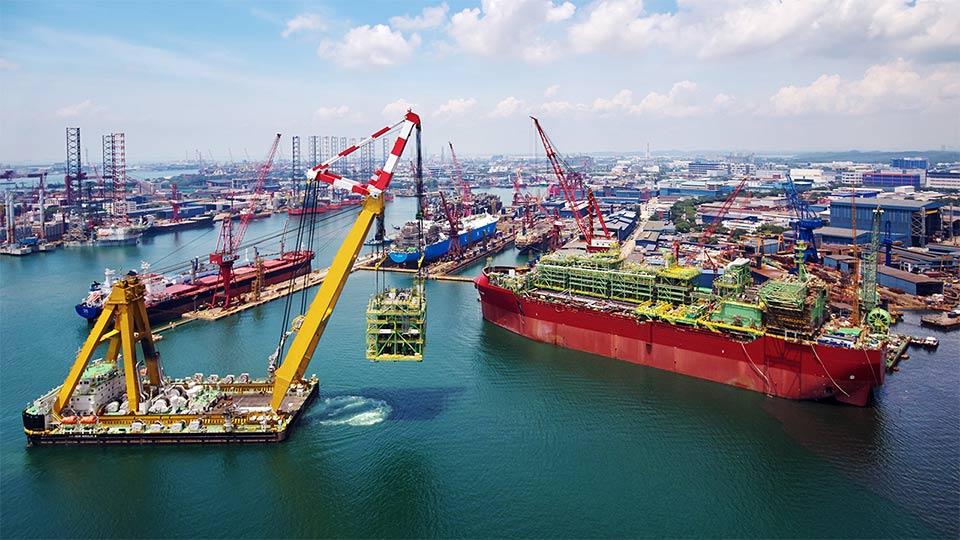
The Process and Flow Technologies yard was just 31 miles from the FPSO integration yard, minimizing transport time and reducing the difficulty of lifting the module onto the vessel.
NOV's internal supply chain helped streamline development and delivery of the module, from proof of concept and design to fabrication at our Process and Flow Technologies yard in Batam, Indonesia. The key location of the facility enabled BW Offshore to easily transport the completed module just 31 miles to the FPSO integration yard in Singapore. The facility's proximity to the integration yard minimized handling of the module, which allowed it to be installed directly onto the FPSO, reducing the burden of transporting such large capital equipment. Another critical aspect of this project was that it combined produced water and seawater treatment, which typically take place in two modules, into one module.
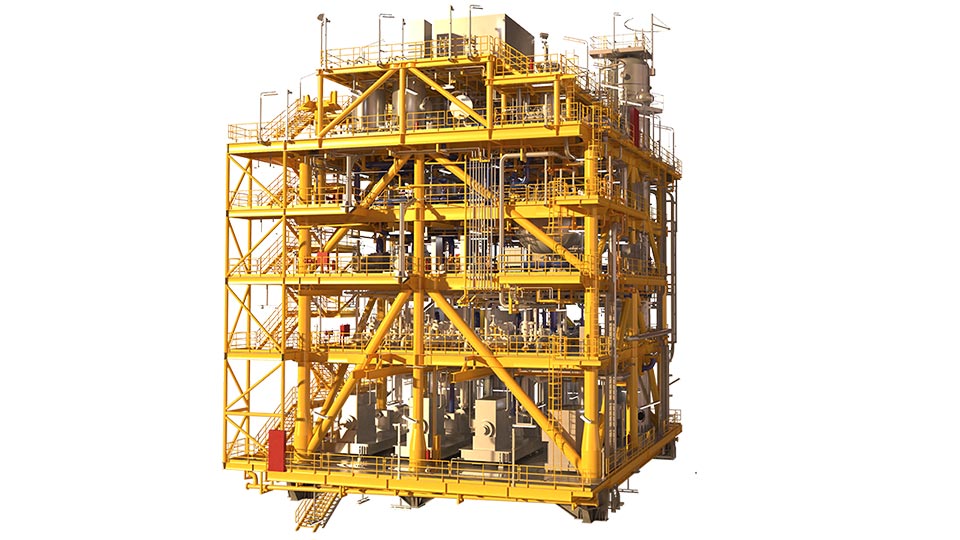
The completed 2-in-1 module combines seawater and produced water treatment in one location, enabling BW Offshore to meet the water-injection requirements of the FPSO over the life of the field.
NOV also delivered 14,232 ft (4338 m) of fiberglass pipe and an APL™ turret and mooring system to complement the water treatment module. In total, employees spent more than 1.2 million man hours on equipment, which was supplied to the vessel with zero lost-time incidents for the entire project. This major accomplishment was the result of close cooperation and vigilance from the safety teams of Premier, BW Offshore, and NOV. NOV received compliments from BW Offshore for piping design and layout as well as work performed on the North Sea compliance documentation that required DNV approval. The final quality of the workmanship of the module was also praised by BW Offshore.
We're proud to have delivered a custom solution to BW Offshore that will help them unlock the full value of this challenging development in the coming years.