Pioneering Spirit was designed to thrive in ruthless ocean environments. This one-of-a-kind vessel performs single-lift installation and removal of large offshore oil and gas platforms, along with installation of oil and gas pipelines. A series of horizontal lifting beams can install platform topsides weighing 48,000 tons (43,545 tonnes) all in one piece and remove 25,000-ton (22,680-tonne) rig jackets in a single lift.
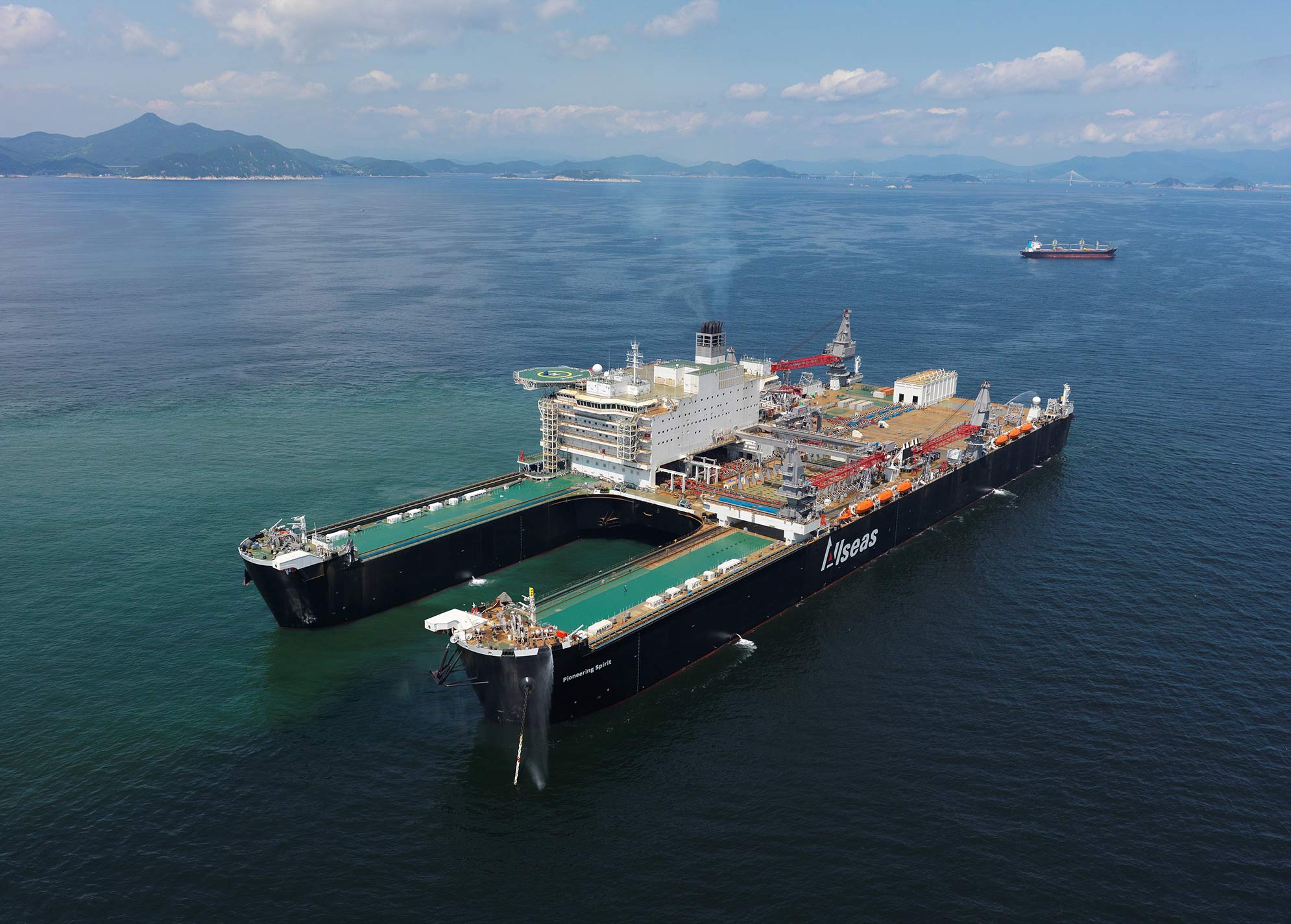
Measuring 1,253 ft (382 m) long and 407 ft (124 m) wide, Pioneering Spirit is almost the size of a floating Empire State Building. At its deepest draft it reaches a world-record displacement of 1 million tons of seawater, making it the heaviest floating object on Earth.
With measurements like these, pulling into a dry dock for repairs isn’t a practical option. The challenge was to build Pioneering Spirit with lighter materials that stopped salt corrosion before it could start.
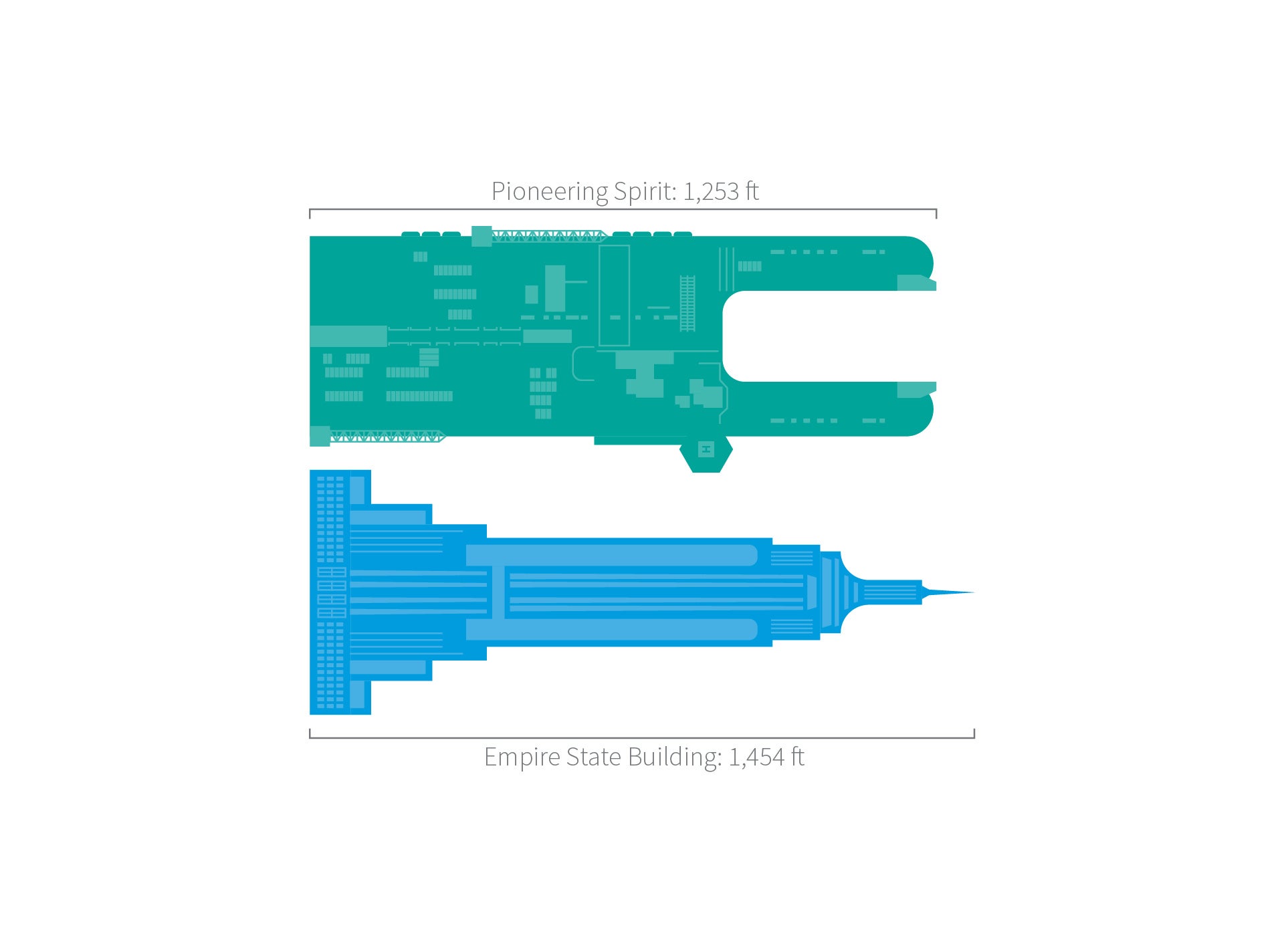
Allseas commissioned NOV's Fiber Glass Systems to build a maintenance-free ballast system to protect their $2.9 billion (€2.6 billion) investment. After intensive review of design specifications, the Bondstrand 2000M pipe series was selected for its corrosion resistance, toughness, and temperature performance. With a projected lifespan of five decades or more, the ballast system will last for the life of the vessel and beyond.
Using detailed pre-design analysis, Fiber Glass Systems produced almost 5 miles of custom fiberglass pipe of various diameters, along with 11,000 fittings. "Just-in-Time" technology delivered materials to the building site right before installation. This approach prevented exposure damage while the pipe spools were in the shipyard, freeing up precious yard space and eliminating warehouse costs.
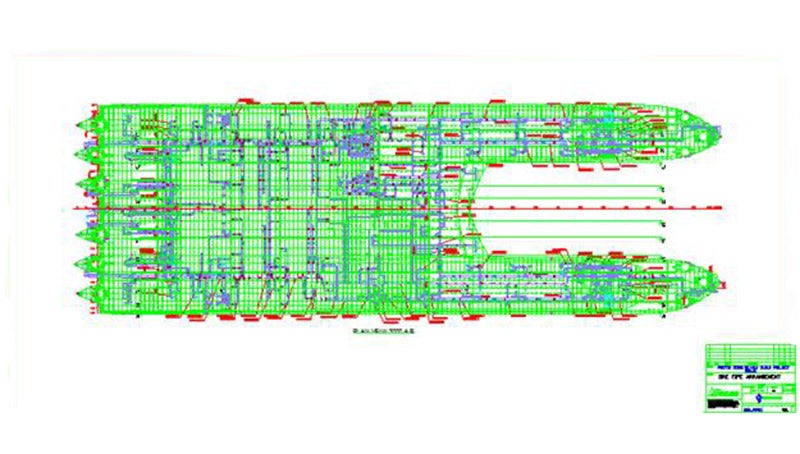
Almost 5 miles of fiberglass pipe (green) were used to construct the ballast system for Pioneering Spirit. (Allseas)
A steel pipe ballast system would have experienced seawater corrosion almost immediately, requiring costly repairs. Pipe replacement has an estimated labor cost of $500 (€443) per foot, not including materials and downtime. Selecting the Bondstrand 2000M pipe potentially saved $50 million (€44 million) in labor cost alone to replace corroded ballast pipe.
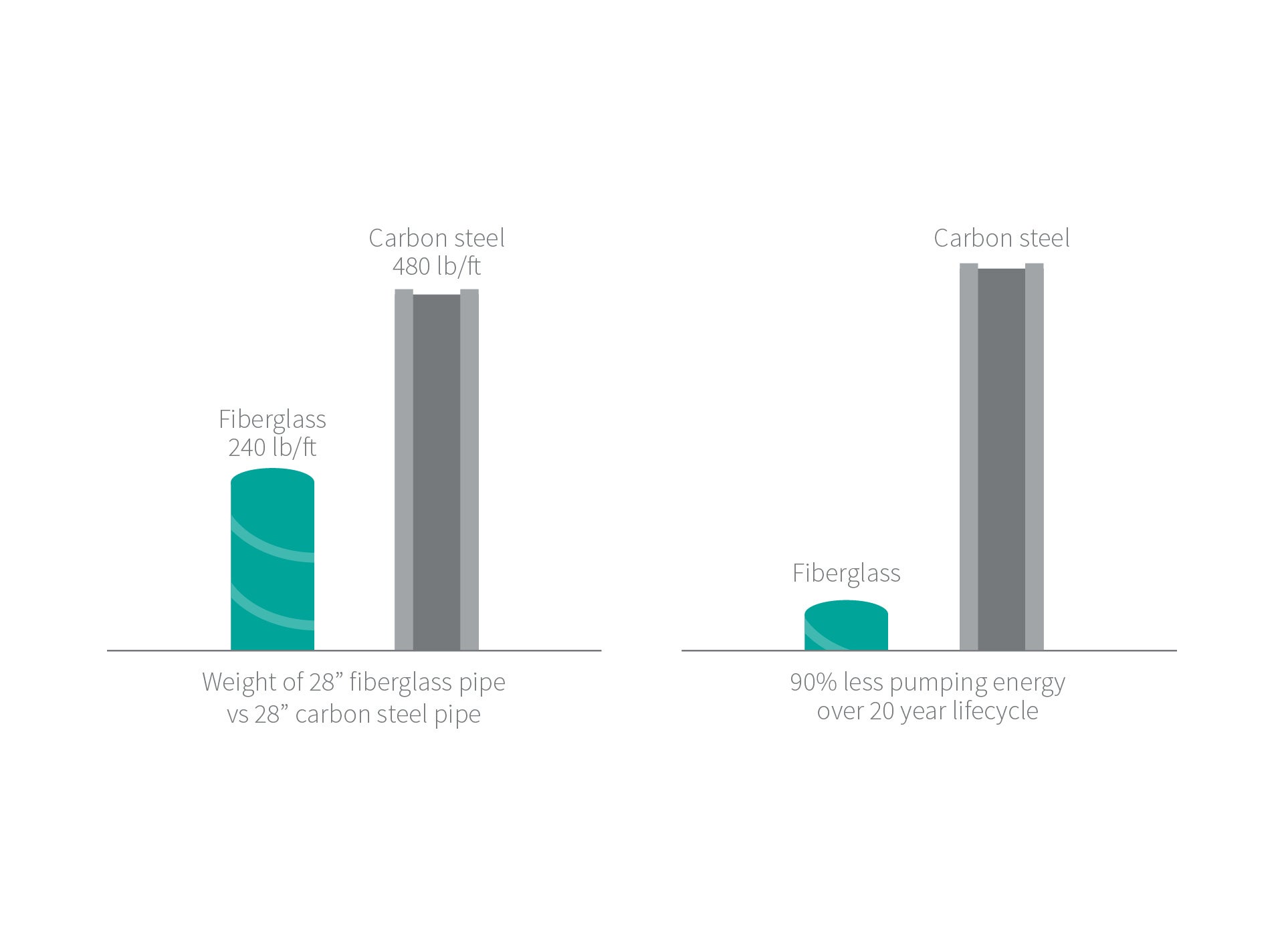
Fiberglass is also a kinder choice for the environment. It eliminates the waste and disposal of replacing steel pipe, saving up to 80% of the energy required to produce new steel pipe. The smoother inner surfaces require less pumping energy, providing up to 90% of energy savings during a 20-year life cycle.
The corrosion-free ballast system forms the strong, pumping heart of Pioneering Spirit. With a life expectancy of more than 50 years, this heart will definitely go on.